the Creative Commons Attribution 4.0 License.
the Creative Commons Attribution 4.0 License.
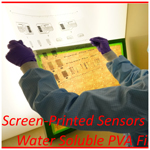
Water transfer printing for integrating substrate-free temperature sensors onto curvilinear surfaces
Jean Charles Fustec
France Le Bihan
Maxime Harnois
This paper presents a reliable emerging technology for fabricating lightweight and conformal temperature-sensing devices on complex shapes and various materials. The process involves screen-printing conductive silver ink with a resistivity of Ωm onto a water-soluble film, followed by a substrate-free transfer. This approach enables the fabrication of flexible temperature sensors on complex surfaces, exhibiting electrical performance comparable to conventional sensors, with a temperature coefficient of resistivity (TCR) of °C−1. Additionally, electrical testing was conducted to validate the stability and reproducibility of the sensors, demonstrating a minimum temperature detection threshold of 0.3 °C.
- Article
(2095 KB) - Full-text XML
- BibTeX
- EndNote
Flexible sensing devices, such as temperature sensors, have gained significant attention due to their ability to bend, enabling them to conform to 3D surfaces (Han et al., 2017). These sensors are widely used across various applications, including robotics (Polygerinos et al., 2017), physiological monitoring (Li et al., 2017), and healthcare (e.g., for body temperature measurements) (Su et al., 2020). High-precision temperature measurements are critical for these applications, necessitating direct contact with the monitored target (e.g., robots or the human body). However, conventional temperature sensors, such as thermocouples, thermistors, and rigid detectors (whether deposited or printed), often require packaging and struggle to maintain conformal contact with uneven surfaces. To enhance the conformability of these detectors, the most reported approach in the literature is to fabricate the sensitive layer on highly deformable thermoplastic polymer, such as polyethylene terephthalate (PET), polyurethane (PU), and silicone elastomers like polydimethylsiloxane (PDMS) (Shih et al., 2010). Even when using an ultra-thin substrate, the sensor remains separated from the target surface as the substrate lies between them. Being built on a 2D flexible surface, the sensor cannot conform to complex 3D shapes without causing the substrate to fold. These challenges are critical in developing conformal, wearable, soft, biocompatible, and lightweight sensors that are state of the art. To address these limitations and to extend the capabilities of traditional electronic design, we introduce an innovative technology that enhances the conformability, lightweight nature, and user-friendliness of sensing devices. This technology, known as water transfer printing (WTP), ensures the substrate-free transfer of highly sensitive temperature sensors onto irregular and curvilinear surfaces without compromising the device's functionality (Le Bihan et al., 2024). As a result, high conformality is achieved as the sensitive film-based temperature sensor is directly applied to the target being monitored, eliminating the need for a plastic substrate. Additionally, WTP enables complex 3D curvilinear surfaces to be effectively functionalized with electronics (Selmi et al., 2023), addressing the challenges previously mentioned.
In this study, we present some electrical characterizations of a transferred silver-based temperature sensor; we begin by detailing the materials and methods employed. Next, we discuss the performance of the sensors, specifically examining their resistance variation as a function of temperature.
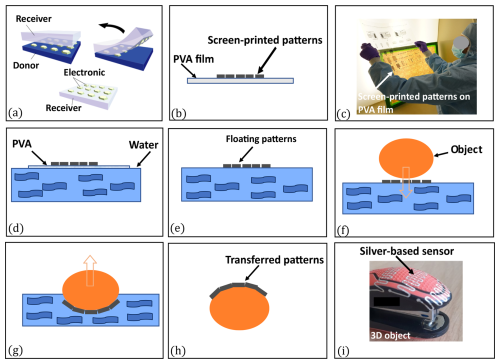
Figure 1(a) Transfer-printing concept. Panels (b) to (h) show the main steps of the WTP process: (b) silver-ink-based sensor screen printed onto a PVA (polyvinyl alcohol) substrate (ink ref: Silver Electron Speedy HR from VFP Ink Technologies), (c) optical picture showing large-area processing of flexible temperature sensors on PVA film, (d) PVA film placed on the water surface, (e) sensor floating after PVA dissolution, (f) object immersed through the sensor, (g) object withdrawn, and (h, i) conformal 3D transfer onto complex 3D objects.
Direct-transfer-printing technology has been extensively developed to transfer electronics onto non-conventional substrates, following the 3D schematic shown in Fig. 1a (Harnois et al., 2020; Herry et al., 2024; Le Borgne et al., 2018, 2019; Rogel et al., 2017; Carlson et al., 2012; Meitl et al., 2006). In this process (see Fig. 1a), the electronic is first fabricated on a donor substrate, which is typically planar, and then is directly transferred onto the target substrate, also known as the receiver. The direct-transfer printing, however, cannot transfer electronics onto the complex 3D object (WTP); a variant of direct-transfer printing addresses this challenge. The manufacturing steps of WTP are illustrated in Fig. 1. First, temperature sensor patterns made of silver ink are screen-printed onto a PVA (polyvinyl alcohol) film (Fig. 1b and c).
This screen-printing process enables large-scale production of temperature sensors on wide surfaces, as shown in Fig. 1c. Then, after curing the ink to remove solvents and to optimize resistivity ( Ωm), the PVA film with the screen-printed patterns is placed onto the surface of the water (Fig. 1d). A few seconds later, the PVA film dissolves, leaving the screen-printed patterns floating on the water's surface (Fig. 1e). A 3D object, intended to receive electronic patterns on its surface, is then immersed in the water (Fig. 1f) and then is removed (Fig. 1g) through the patterns. Finally, the screen-printed patterns are transferred onto the object without a substrate and with high conformality, as shown in Fig. 1h. Note that the adhesion of the ink to the object is optimal, further enhanced by the application of a spray activator, commonly used in graphic arts to improve adhesion strength.
In the WTP process, the activator plays a vital role in transferring rigid electronics onto a substrate. It facilitates the dissolution of the PVA support layer, allowing the electronics to detach and float on the surface of the water. Simultaneously, the activator acts as a plasticizer, softening the adhesive layer to make it temporarily tacky and flexible. This ensures proper adhesion to the object, allowing the electronics to conform smoothly to its shape. The activation process is critical for achieving a strong, uniform bond between the electronics and the substrate. After transferring the electronic patterns forming the sensors onto the object (Fig. 1i), an electrical measurement is performed to validate their proper functioning. The result of this measurement, shown in Fig. 2a, indicates that the transferred sensor works perfectly, with an electrical resistance of 28.5 Ω.
Temperature sensors are an electronic device designed to measure the temperature of an object or a system. That is why the closer the sensor is to the object, the more accurate the measurement will be, which is guaranteed by our process. In Fig. 2b, the I–V characterizations are plotted, showing a linear increase in current versus voltage. This indicates the ohmic behavior of the silver ink. Indeed, sensors fabricated by WTP and those directly screen-printed onto PVA substrate, i.e., before the WTP step, highlight the same electrical behavior.
The resistance variation of the transferred sensor versus temperature is plotted in Fig. 2c. Observing the graph, it is obvious that the resistance of the sensor increases as the temperature increases, following the typical behavior of metallic materials, with a positive temperature coefficient of resistivity (TCR) α, defined as follows:
where R(T) is the resistance at temperature T, and R(T0) is the resistance at the baseline temperature (T0).
From Eq. (1), the TCR of the sensor is estimated to be 3.01×103 °C−1, which is larger than that reported by some commercial standard temperature sensors (Kuo et al., 2012). Note that the authors assume that the transferred silver sensors have been compared to screen-printed ones, demonstrating similar behavior, performance, and sensitivity (0.25 % °C−1).
This is already confirmed by the I–V characterization shown in Fig. 2b (no change in the electrical proprieties).
Figure 3a shows the smallest temperature variation that transferred sensors can reliably detect and measure without applying any complex mathematical treatment. This result demonstrates the sensor's high efficiency and accuracy, enabling it to detect a minimal temperature change of 0.3 °C despite background noise and fluctuations. Moreover, the electrical response of the sensor is reproducible over more than 4 h of cycling, as presented in Fig. 3b.
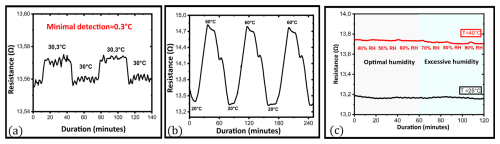
Figure 3(a) Minimal variation in temperature detected by the sensor. (b) Resistance variation of the sensor between 20 and 60 °C for 4 h (sensor reproducibility). (c) Resistance variation of the sensor versus different humidity ratio (sensor stability).
Temperature sensors are placed in locations where temperature needs to be monitored, such as human bodies, industrial environments, air conditioning systems, and medical laboratories. In these application areas, various levels of humidity are defined; in the range of 40 % RH–60 % RH], an environment is considered to be optimal, and in the range of 60 % RH–100 % RH, it is considered to be very humid. Figure 3c shows the impact of humidity on the transferred temperature sensor described previously.
The result highlights that the sensor is not sensitive to humidity (for neither an optimal humidity level or an excessive one) regardless of the temperature value (25 or 40 °C). This ensures the normal behavior and stability of the transferred temperature sensor in all desired installation environments, disregarding the humidity effect.
In summary, the WTP process surpasses the limits of traditional electronic manufacturing by enabling the transfer of temperature sensors onto all complex objects regardless of their shapes while obviously maintaining the same performance as conventional sensors. Thus, the TCR remains stable on the final structure, as evidenced by the preservation of the sensor's resistivity before and after the transfer (see Fig. 2b). Additionally, electrical tests conducted several years after the transfer process confirm the sensor's proper functioning and stability. No additional measures were taken to protect the sensor from degradation caused by external environmental factors. If required, an insulating encapsulation layer can be screen-printed over the sensor's functional layer. This would ensure an extended lifespan, as typically achieved with metallic sensors.
Finally, the WTP process appears to be highly promising for the field of lightweight and conformal electronics and can be applied in various other fields such as wearable electronics, plant bio-electronics, and bio-hybrid systems. Note that the silver-sensitive layer that forms the sensor performs effectively within a temperature range below 0 °C and can tolerate temperatures of up to 200 °C. However, it is crucial that the 3D object onto which the sensor is applied can also withstand this temperature range. Moreover, humidity, as an environmental factor, was tested on the sensor, and the results showed no significant sensitivity to it (see Fig. 3c). As a result, resistivity and TCR remain unaffected. However, with regard to other parameters, such as gas concentration and thermal radiation, their impact cannot be determined without further experiments. Based on the current understanding, it is recommended that one perform the transfer process in a controlled environment that is kept at 20 °C and that is free from concentrated gases and thermal radiation, as well as on a dry object. These experiments could be part of our future work.
All measurements and experimental datasets are publicly available in the text (Figs. 1–3). Further requests can be directed to the corresponding author.
RS conducted the fabrication and electrical characterization of the devices and wrote and edited the paper. JCF participated in the fabrication process. FLB and MH supervised the work and reviewed the paper.
The contact author has declared that none of the authors has any competing interests.
Publisher's note: Copernicus Publications remains neutral with regard to jurisdictional claims made in the text, published maps, institutional affiliations, or any other geographical representation in this paper. While Copernicus Publications makes every effort to include appropriate place names, the final responsibility lies with the authors.
This article is part of the special issue “Eurosensors 2024”. It is a result of the EUROSENSORS XXXVI, Debrecen, Hungary, 1–4 September 2024.
The authors thank the NanoRennes platform belonging to RENATECH+ (French National Network of Facilities for Micro and Nanotechnology). This publication is supported by the European Union through the European Regional Development Fund (ERDF) and by the Ministry of Higher Education and Research, Brittany and Rennes Metropole, through the CPER Projects SOPHIE/STIC & Ondes and MAT&TRANS.
This research has been supported by the NanoRennes plateform.
This paper was edited by Gabor Battistig and reviewed by two anonymous referees.
Carlson, A., Bowen, A. M., Huang, Y., Nuzzo, R. G., and Rogers, J. A.: Transfer Printing Techniques for Materials Assembly and Micro/Nanodevice Fabrication, Adv. Mater., 24, 5284–5318, https://doi.org/10.1002/adma.201201386, 2012.
Han, S., Peng, H., Sun, Q., Venkatesh, S., Chung, K., Lau, S. C., Zhou, Y., and Roy, V. A. L.: An Overview of the Development of Flexible Sensors, Adv. Mater., 29, 1700375, https://doi.org/10.1002/adma.201700375, 2017.
Harnois, M., Garcia-Castro, F., Herry, G., De Sagazan, O., and Le Bihan, F.: Eco-designed Conformable Inorganic Electronics to Improve the End of Life of Smart Objects: Sensor Processing and Applications, ACS Appl. Electron. Mater., 2, 563–570, https://doi.org/10.1021/acsaelm.9b00807, 2020.
Herry, G., Fustec, J.-C., Le Bihan, F., and Harnois, M.: Substrate-Free Transfer of Silicon- and Metallic-Based Strain Sensors on Textile and in Composite Material for Structural Health Monitoring, ACS Appl. Mater. Interf., 16, 22113–22121, https://doi.org/10.1021/acsami.4c01055, 2024.
Kuo, J. T. W., Yu, L., and Meng, E.: Micromachined Thermal Flow Sensors – A Review, Micromachines, 3, 550–573, https://doi.org/10.3390/mi3030550, 2012.
Le Bihan, F., Selmi, R., C. Fustec, J., and Harnois, M.: PT3.49 – Water Transfer Printing of Silver Ink-based Temperature Sensors, in: Poster, EUROSENSORS XXXVI, 1–4 September 2024, Debrecen, Hungary, 273–274, https://doi.org/10.5162/EUROSENSORSXXXVI/PT3.49, 2024.
Le Borgne, B., Jacques, E., and Harnois, M.: The Use of a Water Soluble Flexible Substrate to Embed Electronics in Additively Manufactured Objects: From Tattoo to Water Transfer Printed Electronics, Micromachines, 9, 474, https://doi.org/10.3390/mi9090474, 2018.
Le Borgne, B., Chung, B.-Y., Tas, M. O., King, S. G., Harnois, M., and Sporea, R. A.: Eco-Friendly Materials for Daily-Life Inexpensive Printed Passive Devices: Towards “Do-It-Yourself” Electronics, Electronics, 8, 699, https://doi.org/10.3390/electronics8060699, 2019.
Li, Q., Zhang, L., Tao, X., and Ding, X.: Review of Flexible Temperature Sensing Networks for Wearable Physiological Monitoring, Adv. Healthc. Mater., 6, 1601371, https://doi.org/10.1002/adhm.201601371, 2017.
Meitl, M. A., Zhu, Z.-T., Kumar, V., Lee, K. J., Feng, X., Huang, Y. Y., Adesida, I., Nuzzo, R. G., and Rogers, J. A.: Transfer printing by kinetic control of adhesion to an elastomeric stamp, Nat. Mater., 5, 33–38, https://doi.org/10.1038/nmat1532, 2006.
Polygerinos, P., Correll, N., Morin, S. A., Mosadegh, B., Onal, C. D., Petersen, K., Cianchetti, M., Tolley, M. T., and Shepherd, R. F.: Soft Robotics: Review of Fluid-Driven Intrinsically Soft Devices; Manufacturing, Sensing, Control, and Applications in Human-Robot Interaction, Adv. Eng. Mater., 19, 1700016, https://doi.org/10.1002/adem.201700016, 2017.
Rogel, R., Borgne, B. L., Mohammed-Brahim, T., Jacques, E., and Harnois, M.: Spontaneous Buckling of Multiaxially Flexible and Stretchable Interconnects Using PDMS/Fibrous Composite Substrates, Adv. Mater. Interf., 4, 1600946, https://doi.org/10.1002/admi.201600946, 2017.
Selmi, R., Fustec, J.-C., Harnois, M., and Bihan, F. L.: Organic and Metallic Sensors on Complex 3-D Object Using an Original Method: Water Transfer Printing, IEEE Sens. Lett., 7, 1–4, https://doi.org/10.1109/LSENS.2023.3301845, 2023.
Shih, W.-P., Tsao, L.-C., Lee, C.-W., Cheng, M.-Y., Chang, C., Yang, Y.-J., and Fan, K.-C.: Flexible Temperature Sensor Array Based on a Graphite-Polydimethylsiloxane Composite, Sensors, 10, 3597–3610, https://doi.org/10.3390/s100403597, 2010.
Su, Y., Ma, C., Chen, J., Wu, H., Luo, W., Peng, Y., Luo, Z., Li, L., Tan, Y., Omisore, O. M., Zhu, Z., Wang, L., and Li, H.: Printable, Highly Sensitive Flexible Temperature Sensors for Human Body Temperature Monitoring: A Review, Nanosc. Res. Lett., 15, 200, https://doi.org/10.1186/s11671-020-03428-4, 2020.